MCG 1000
Multifunctional machining centre MCG 1000i (3- to 6-axis solution)
The MCG 1000 machine is a multifunctional machining centre of upper gantry-type designed for complex machining of spatially complicated and technologically demanding workpieces as well as of combined shapes, both within five-axis milling operations and full-featured turning operations.
The centre enables milling in five axes, namely in three mutually perpendicular coordinate axes X, Y, Z, in the rotary C-axis – a rotary tilting table with built-in torque motor enabling turning operations, and in the tilting B-axis – a rotary tilting table with built-in torque motors. It is a highly productive machine characterized by high dynamic and thermal stability and high accuracy of machining. Every working axis is travelling along linear guide-ways. A direct measuring system in all axes is a part of the basic configuration.
The machine is intended for production of metallic parts for pressing, plastic-making, automotive and aviation industry. It is also well-suited for standard machining. It enables machining a workpiece from five sides. It allows milling, drilling, boring, reaming, thread cutting and turning technological operations. Featuring a 12000 rpm spindle and utilizing ring motors in the rotary axes, the machine fully supports shape machining and HSC machining. The maximal diameter of the workpiece can be 1 000 mm, with weight of 1 300 kg for milling operations and 700 kg for turning operations.
Standard equipment:
- Sinumerik 840D SL / Heidenhain TNC 640 / FANUC control system
- electrospindle with maximal speed of 15 000 rpm
- ISO 40 clamping taper
- continuously controlled rotary-tilting table of Ø 800 mm
- digital feed drives
- one tool changer for 50 tool
- Heidenhain direct measuring system
- pneumatic elements
- central lubrication system
- tool holder automatic air-blasting
- cooling unit with tool outer cooling system
- spindle thermal stabilization
- chip conveyor
- electronic handwheel
- vibrodiagnostics
Optional equipment:
- spindle units
- cooling through spindle axis of AD type – coolant, filtering unit
- electrical cabinet air conditioning
- cooling through spindle axis of AD type – air
- workpiece dimensions measuring probe
- tool measuring probe
- exhaustion of oil-mist from workzone
- oil-mist cooling
- work table of Ø 1 000 mm
- handheld wash-out gun
- remote diagnostic installation
- machine hibernation
- technological software
- digital handwheel
- visiport
- work cycle signalling
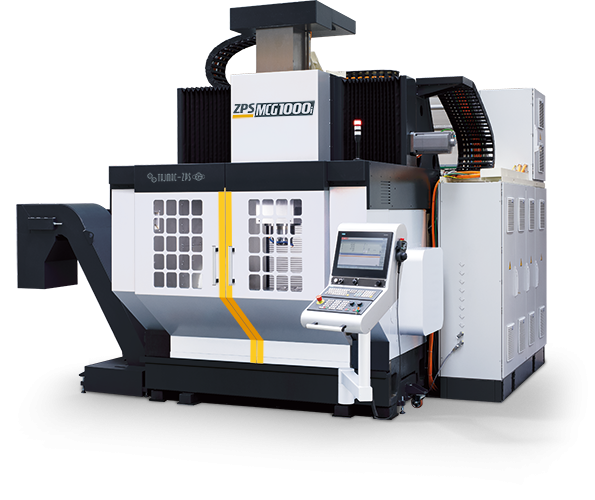
MCG 1000
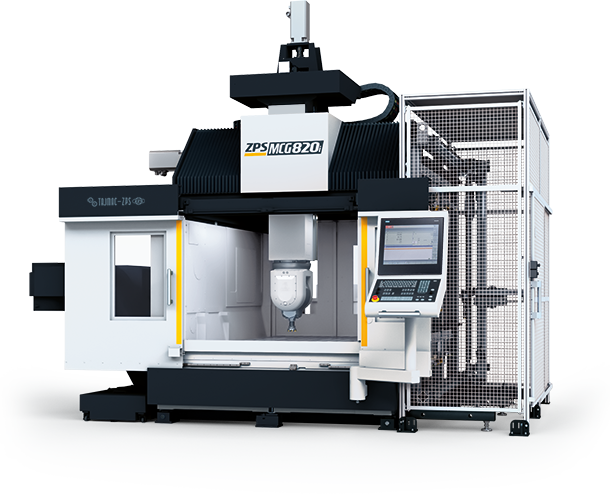
MCG 820

MCG 810
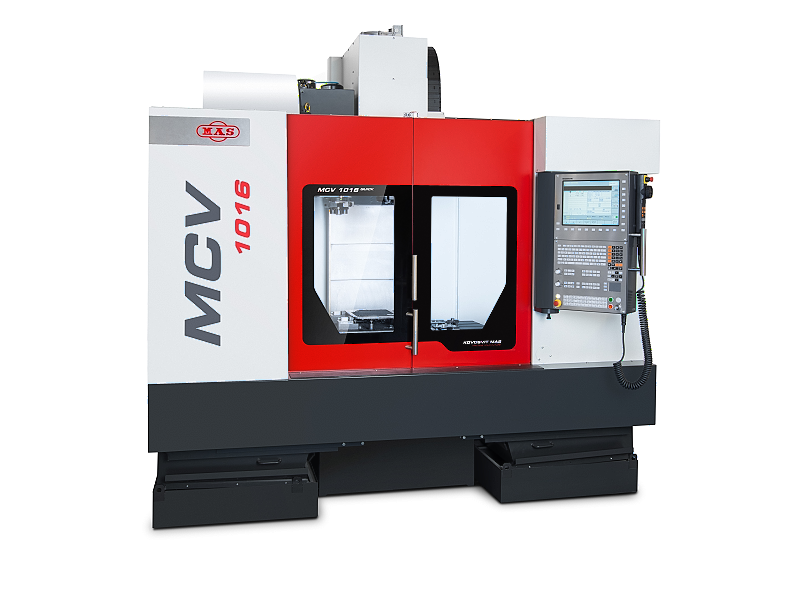
MCV 1016 Quick
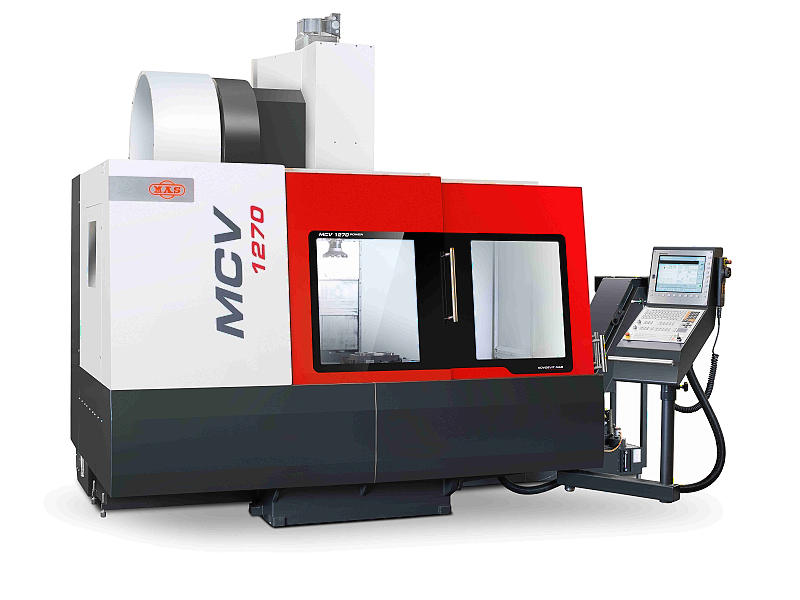
MCV 1270 Rapid / Sprint / Speed / Power
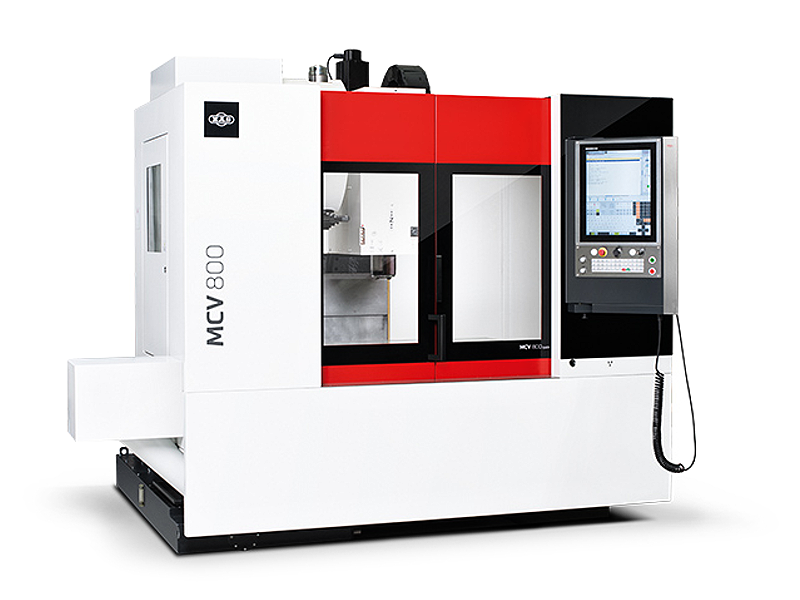
MCV 800 Quick
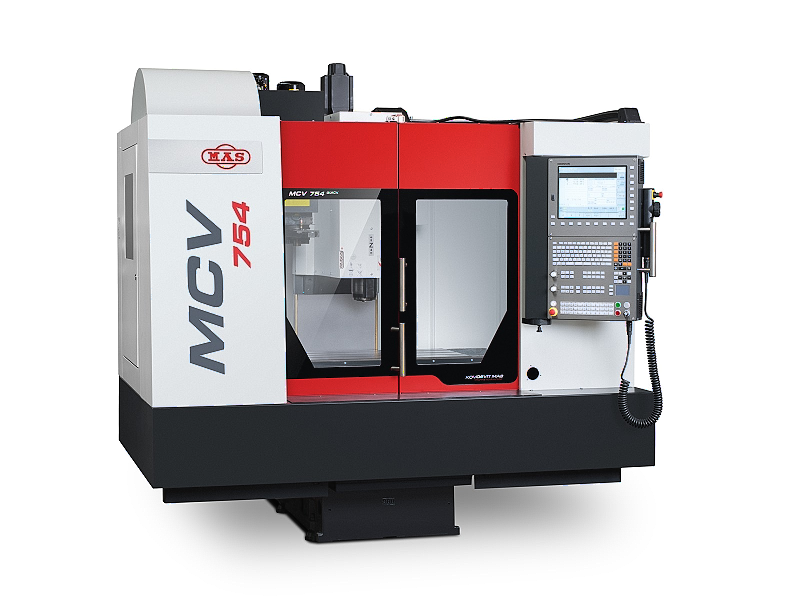
MCV 754 Quick
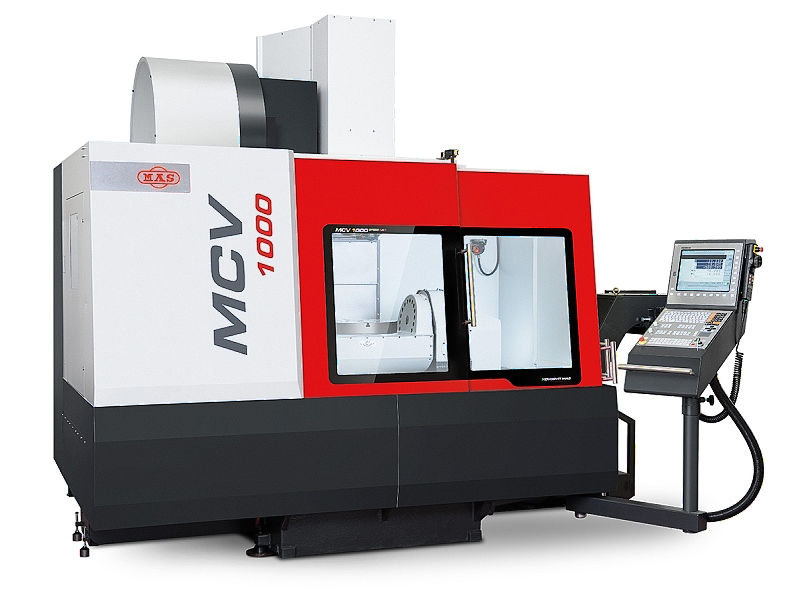
MCV1000 Rapid / Sprint / Speed / Power
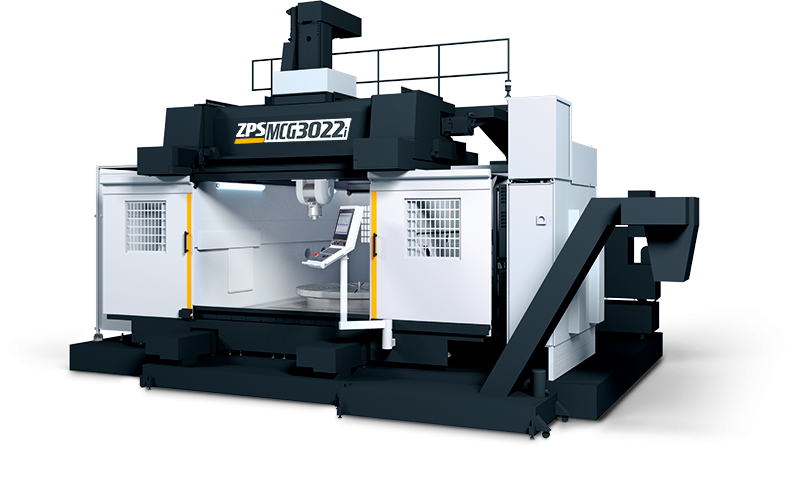
MCG 3022
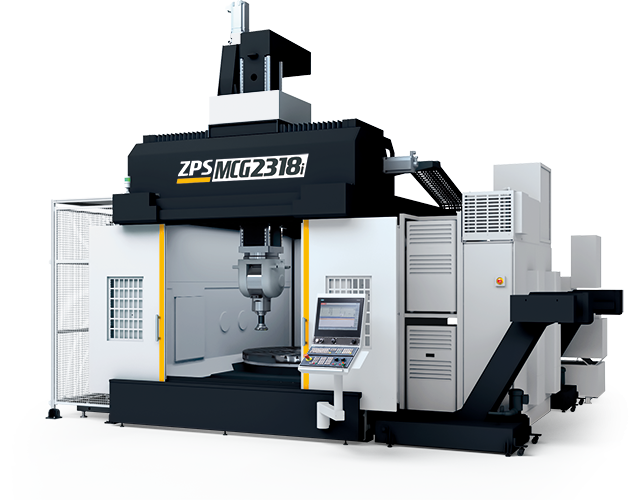