Request
SBX 500 CNC
SBX 500 CNC - Turning center for effective production and high productivity achievement. Optimized design of the machine carrier structure, Y axis on saddle wedge principle in combination with linear roller guide ways guarantee high rigidity, constant repeatable precision and maximum machining stability.
CNC turning center SBX 500
SBX 500 CNC – Turning center for effective production and high productivity achievement. Optimized design of the machine carrier structure, Y axis on saddle wedge principle in combination with linear roller guide ways guarantee high rigidity, constant repeatable precision and maximum machining stability. The variability of modular conception allows flexible adaptation of machine configuration to customers’ demands.
Most important features:
- Modular conception allows configuring the machine for wide range of technologies and materials
- Counter spindle with passing hole clamping allows complete machining
- Y axis with saddle wedge contributes to increased stability of cutting process
- Fast turret with 12 live tools size VDI 40
- C-axes with independent servomotors for achieving precise and stabile work piece position during cutting forces loading
- Linear roller guide ways with bearing capacity dimensioned for hard roughing but also precision of finishing operations
- Increased spindle bores extend the machining possibilities for wider assortment of work pieces
- Integrated control panel improves machine control ergonomics for operator
- Programming in 3D through cycles
- Technology of servo drives with electric energy saving
- Option of industrial robot integration for manipulation of raw material and work pieces
- Coolant aggregate with pressure from 0.7 MPa (7 bar) up to 2.0 MPa (20 bar)
Basic execution:
- Control system SIEMENS Sinumeric 840D SolutionLine, software Operate
- Digital servo drives SIEMENS Sinamics S120 with energy recovery
- Vector controlled asynchronous motor for main spindle drive 22 kW
- Direct angle and rotation measuring through magnetic disc sensor integrated in the main spindle
- C-axis of the main spindle positioned through the motor of the main spindle
- Main spindle bore 92 mm
- Hydraulic 3-jaw chuck dia. 254 mm, with through hole dia. 75 mm max. 4000 RPM for main spindle
- Electronic check of hydraulic clamping limit positions
- Security locking system for hydraulic clamping systems of the main spindle
- Double foot switch to open/close chuck of the main spindle
- Main spindle brake
- Programmable tailstock
- Turning length between chuck and tailstock 800 mm
- Y-axis travel ± 60 mm
- Linear rolling guide ways
- Direct X-axis measurement by linear scale
- Automatic lubrication with controlled distribution of lubricant
- 12-position fast axial turret, VDI40 with live tools
- Chip conveyor to the right side
- Complete cooling aggregate pressure 0,7 MPa (7 bar)
- Manual door opening
- Positionable control panel
- Entering input and output parameters in metric/imperial units
- Voltage 3×400V /50Hz
- Transporting device
- Operating manual
- “CE” execution
Modular executions:
- C-axis of the main spindle positioned by separate servomotor connected through reduction gear
- I ncreased main spindle bore 133 mm, hydraulic 3-jaw chuck, dia. 315 mm with through hole 117 mm, max. 2800 RPM
- Pneumatic blow-out for chuck
- Direct measuring of Z-axis by linear scale
- Direct measuring of Y-axis by linear scale
- Counter spindle execution, C-axis for counter spindle positioned by counter spindle motor
- Vector controlled asynchronous motor for counter spindle 9 kW
- Direct angle and rotation measuring through magnetic disc sensor integrated in the counter spindle
- Electronic check of hydraulic clamping limit positions
- Security locking system for hydraulic clamping systems of the counter spindle
- Double foot switch to open/close chuck of the counter spindle
- Counter spindle brake
- Turning length between main and counter chuck 650 mm
- Counter spindle bore 65 mm, hydraulic 3-jaw chuck, dia. 210 mm, with through hole 51 mm, max. 4000 RPM
- I ncreased counter spindle bore 92 mm, hydraulic 3-jaw chuck, dia. 254 mm, with through hole 75 mm, max. 3500 RPM
- C-axis of the counter spindle positioned by separate servomotor connected through reduction gear
- Direct measuring of Z2 axis by linear scale (counter spindle travel)
- Hydraulic collet clampings of various sizes for both spindle bore sizes of main and counter spindle
- 12-position fast radial turret, size VDI40 with live tools
- Coolant filtration
- Manual wash
- Oil mist filtration
- Automatic door opening (pneumatic)
- Air conditioning for electrocabinet
- Preparation for bar feeder
- Bar feeder
- Parts catcher
- Tool probe
- Work piece probe
- Remote diagnostics
- Autotransformer for 220 V or 575 V
- 3-colour warning light (machine process stage signalization)
- Chip conveyor to the rear side of the machine
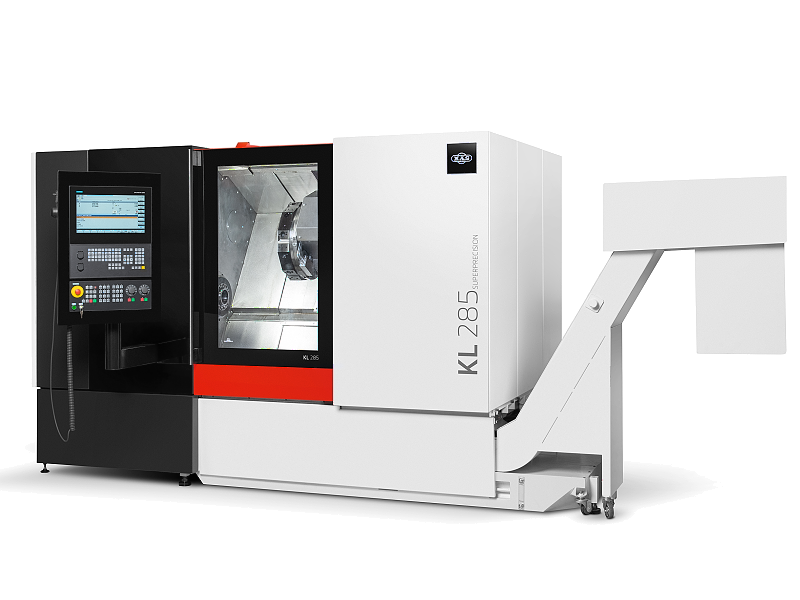
KL285
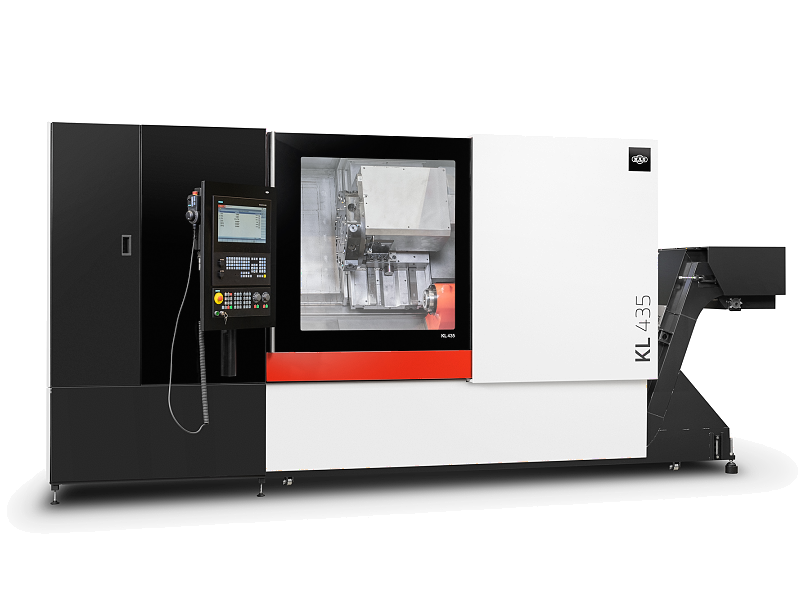
KL435
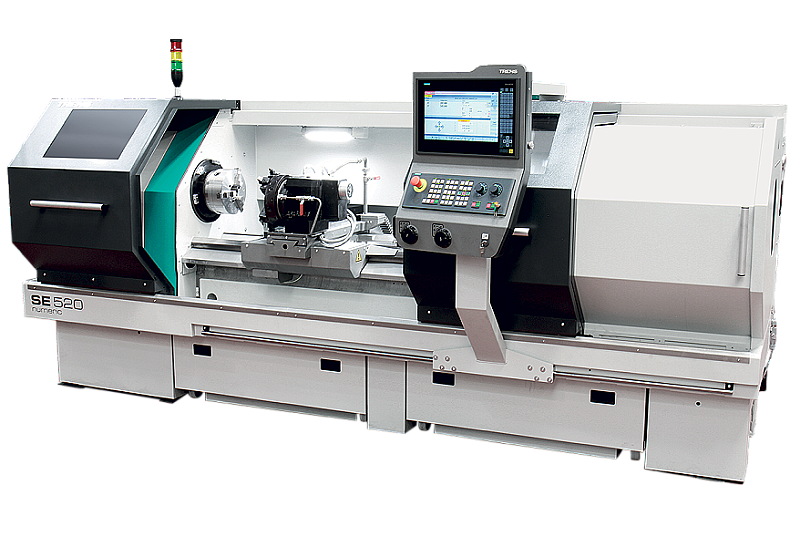
SE520 SL
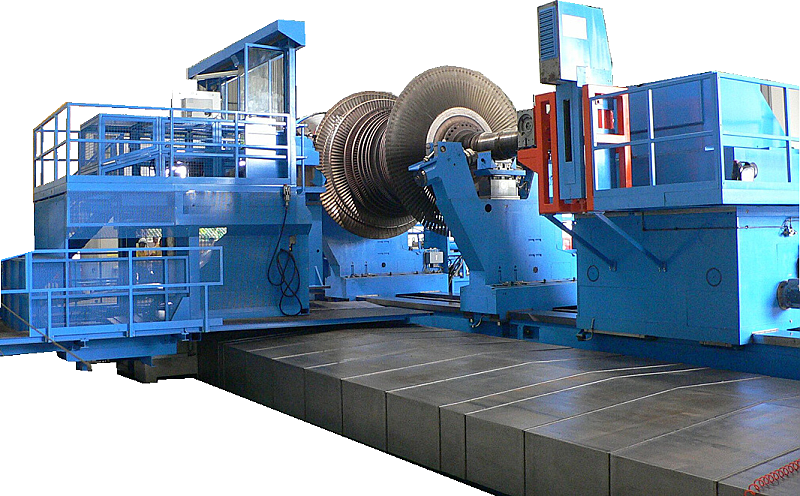
SR1, SR2, SR3, SR4, SR5
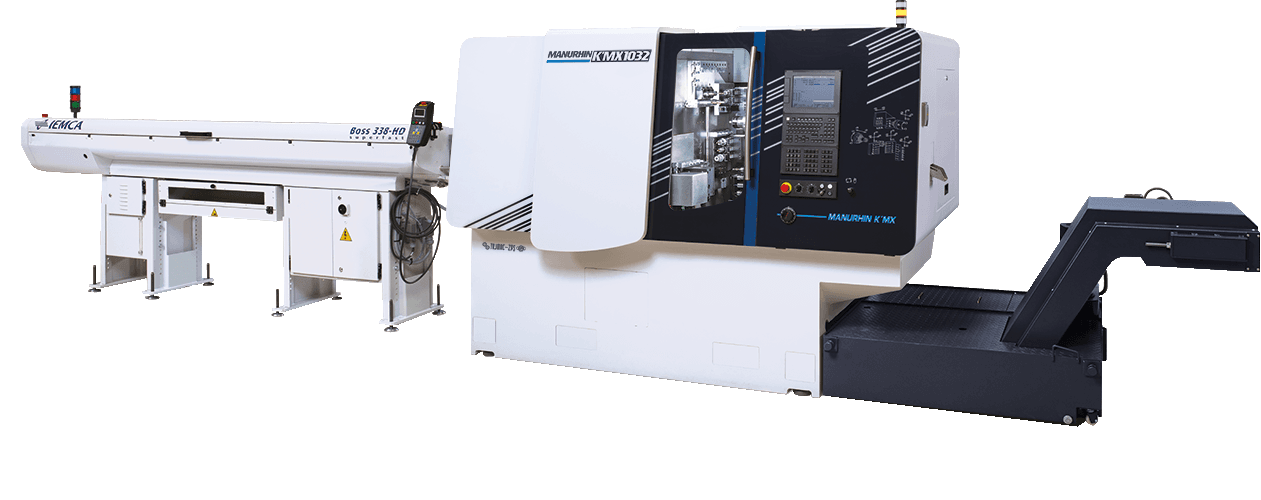
MANURHIN K’MX 1032
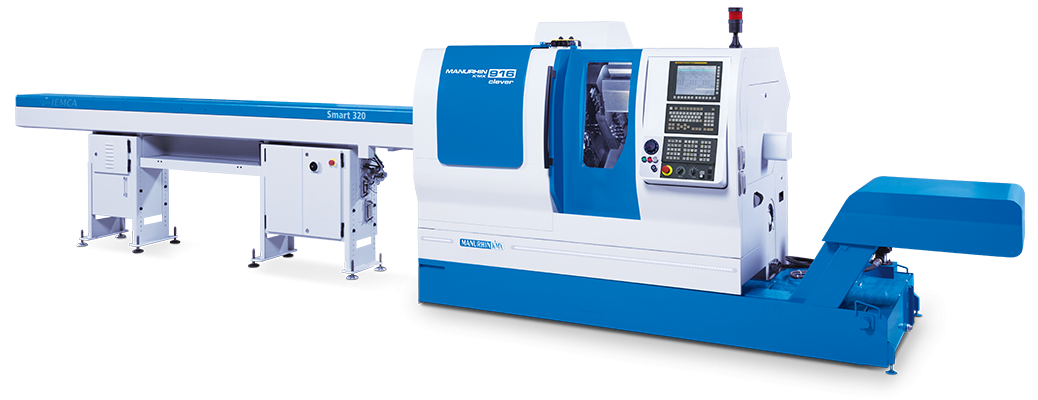
MANURHIN K’MX 916 CLEVER
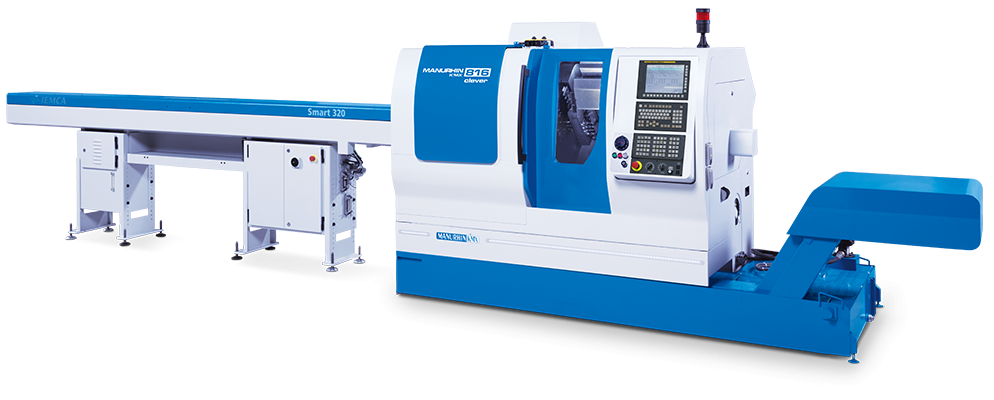
MANURHIN K´MX816 CLEVER
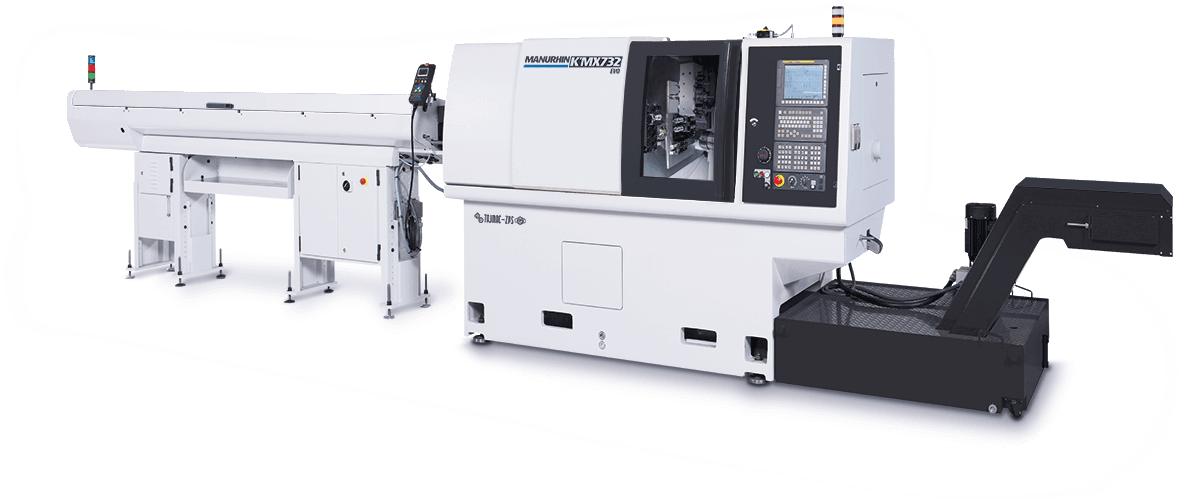
MANURHIN K´MX732EVO
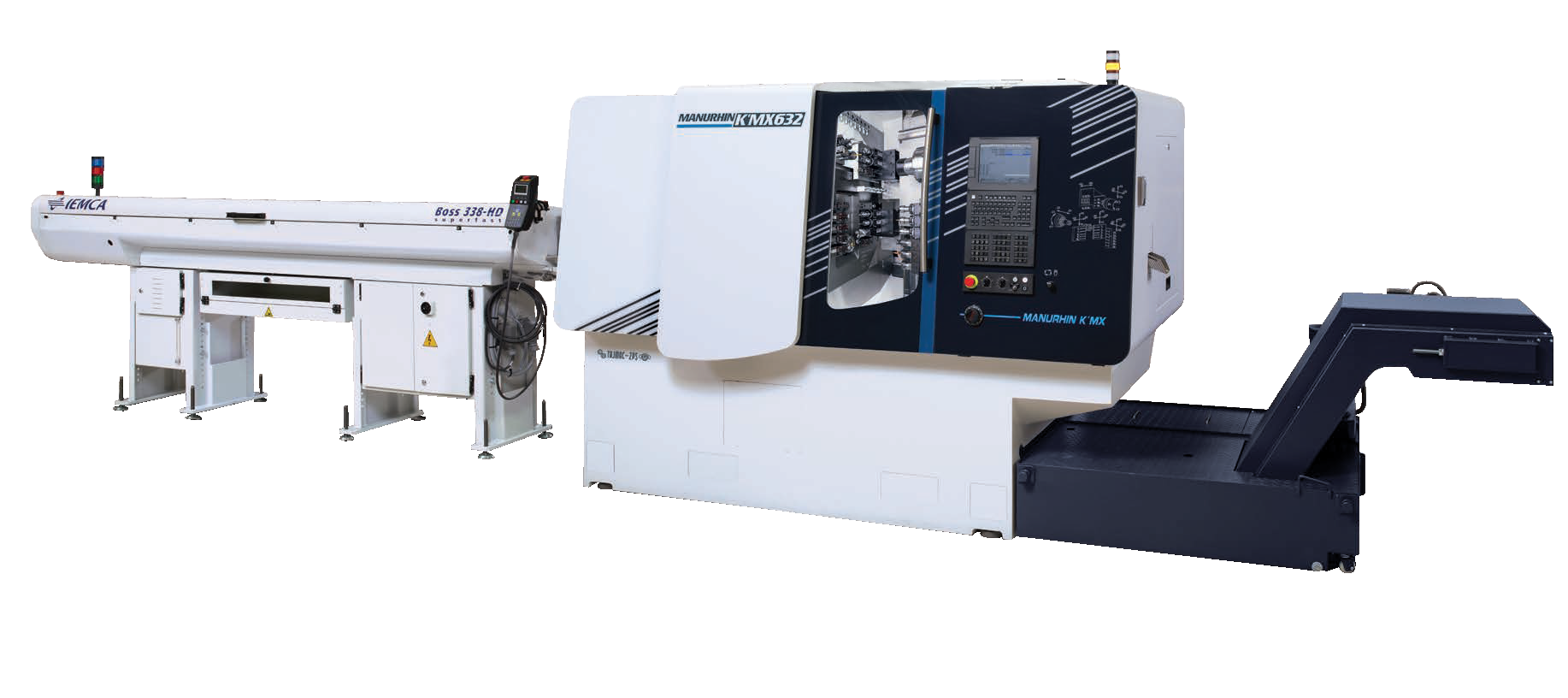
MANURHIN K´MX632DUO
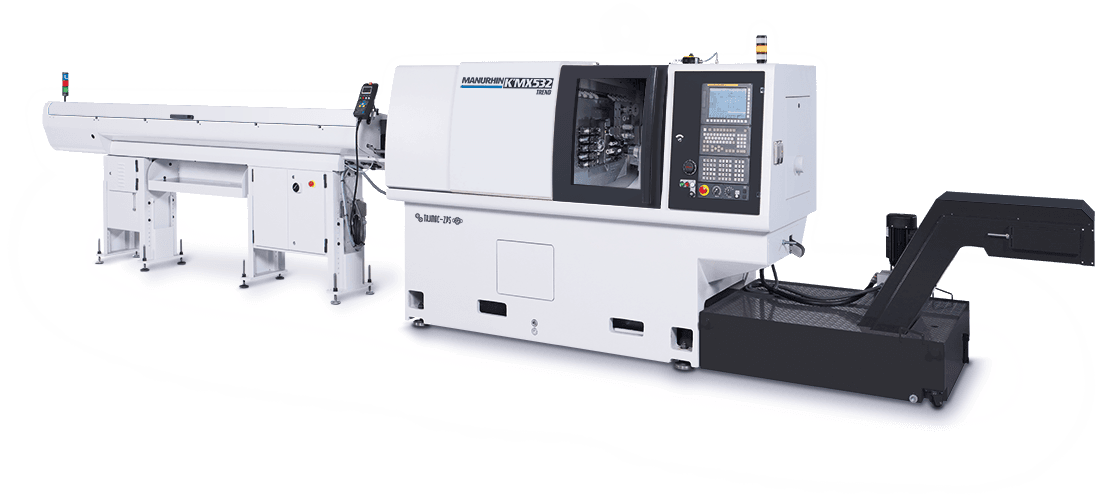
MANURHIN K´MX532 TREND
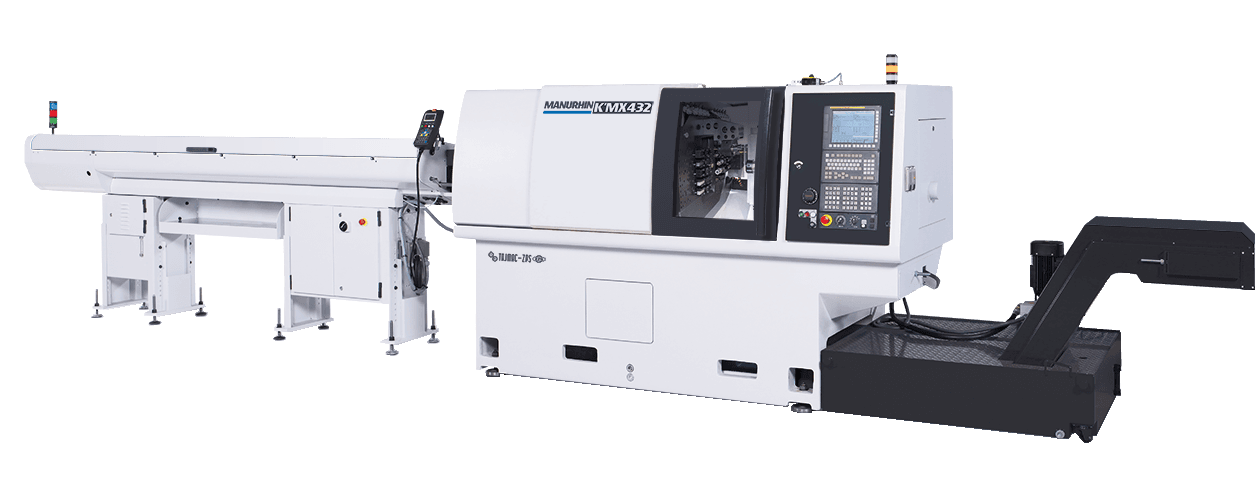
MANURHIN K´MX432
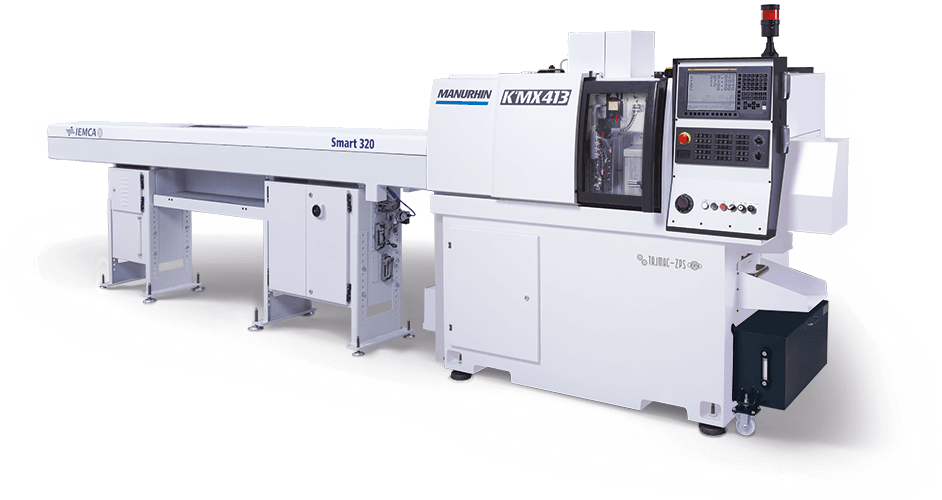
MANURHIN K´MX413
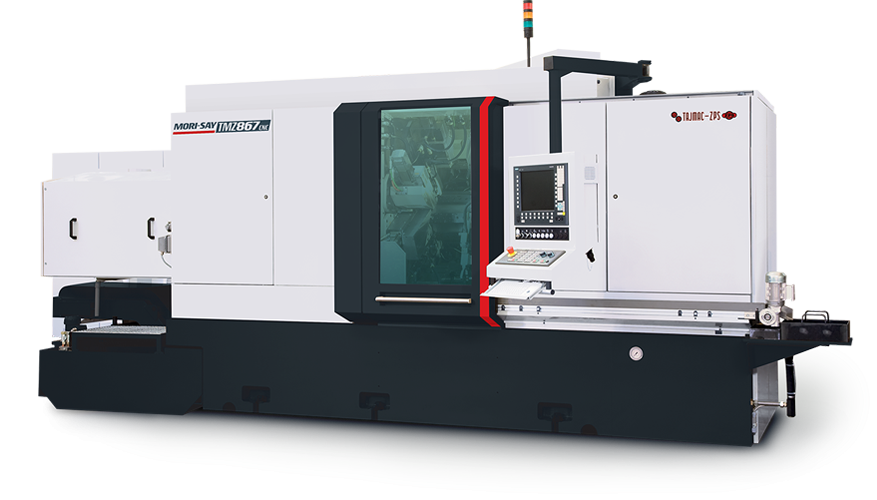
MORI-SAY TMZ867 CNC
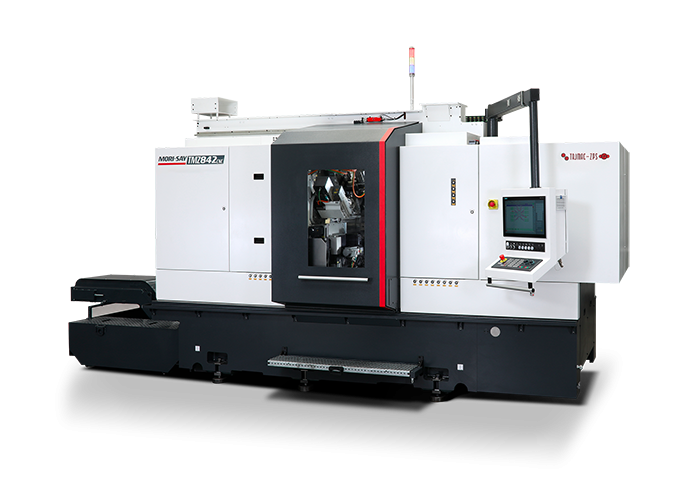
MORI-SAY TMZ842 CNC
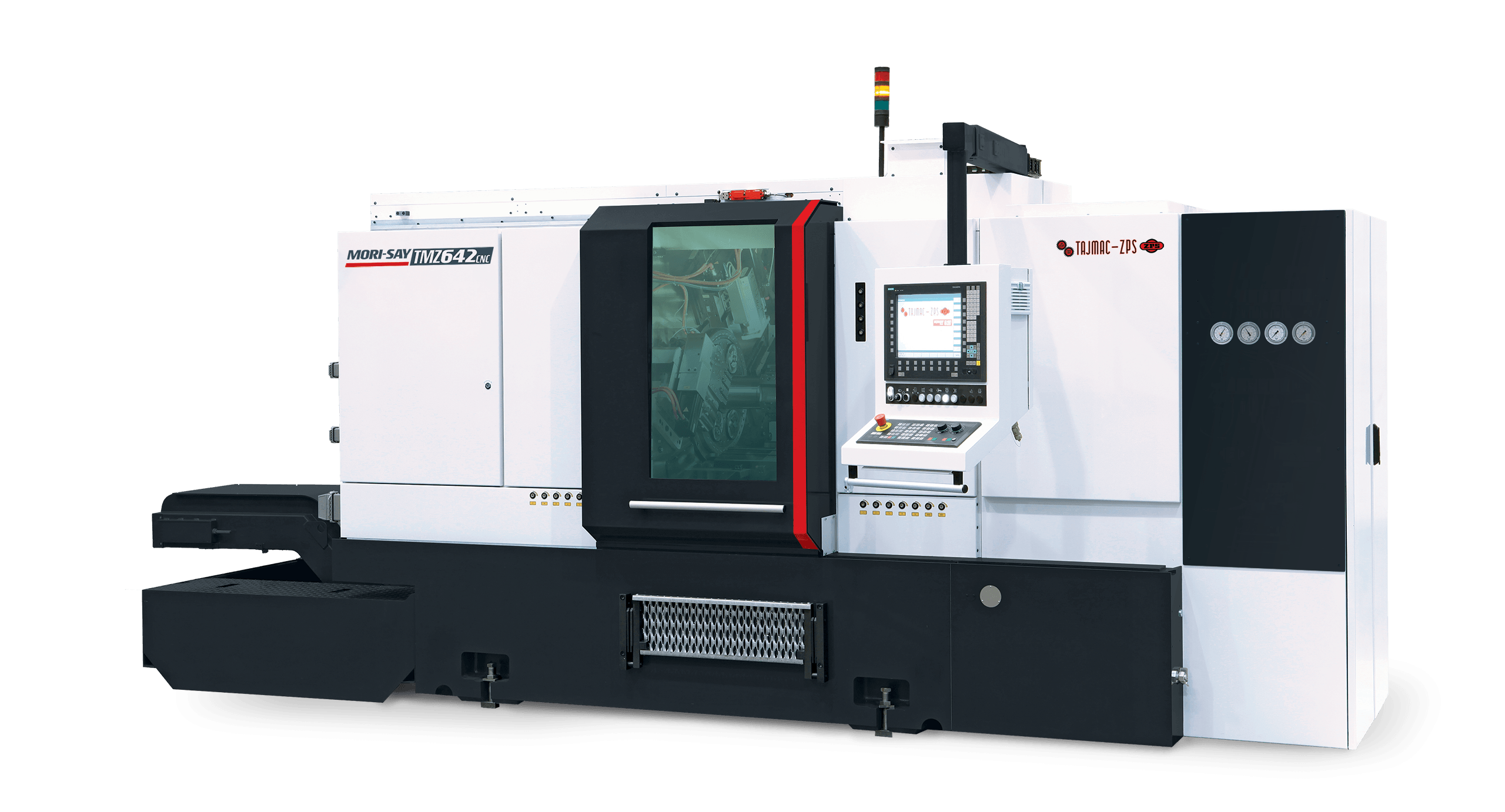
MORI-SAY TMZ642 CNC
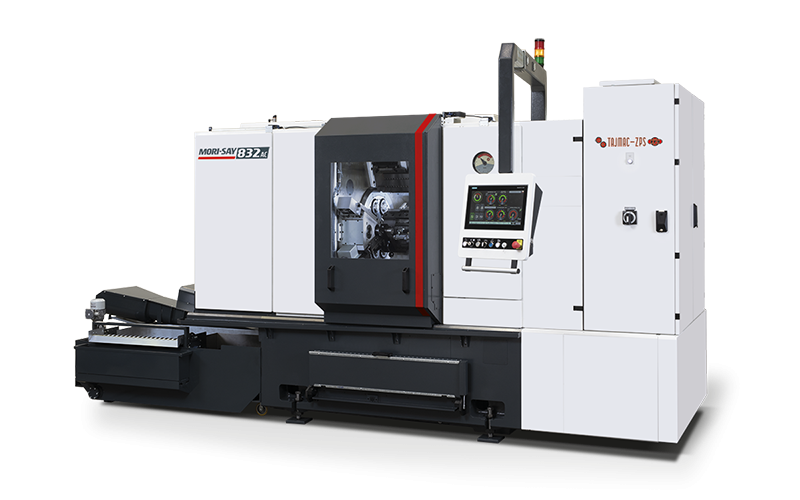
MORI-SAY 832AC / 842AC
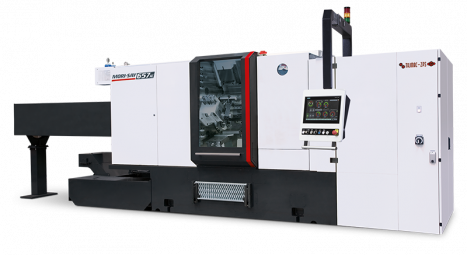
MORI-SAY 657AC, 667AC
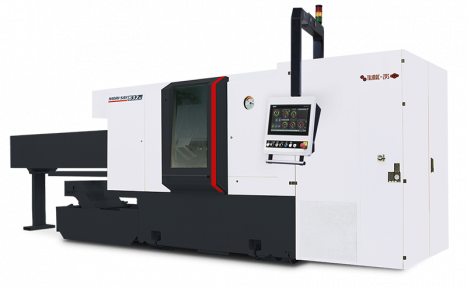
MORI-SAY 632AC / 642AC
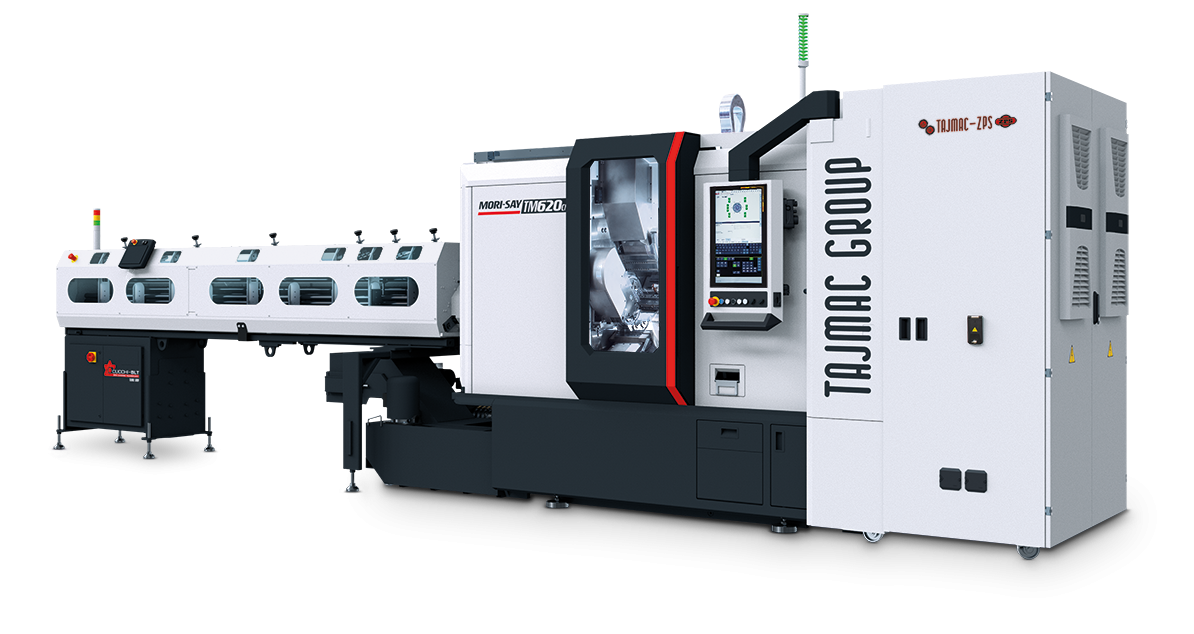
MORI-SAY 620AC
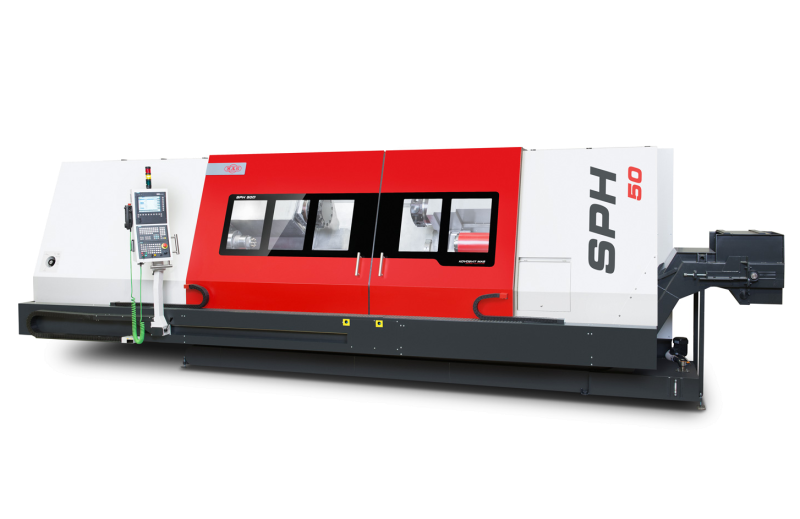
SPH 50 / D / DS
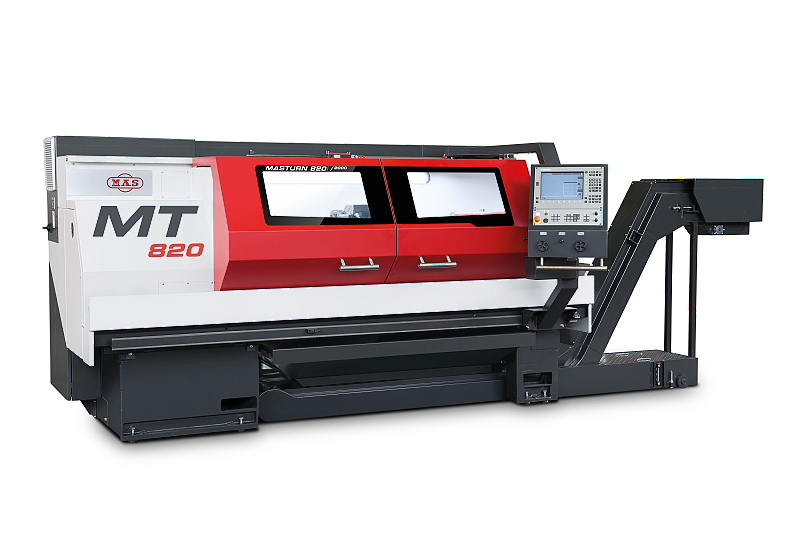
MASTURN
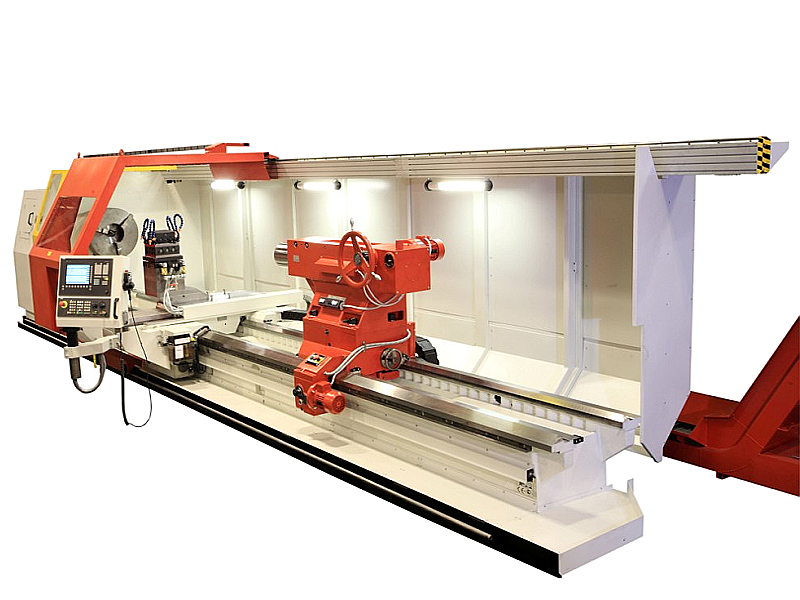
SUA 150 Numeric
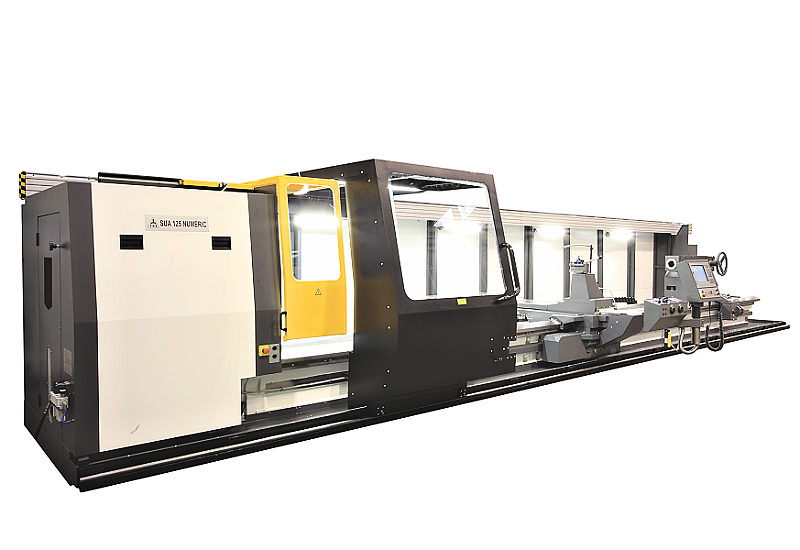
SUA 125 Numeric
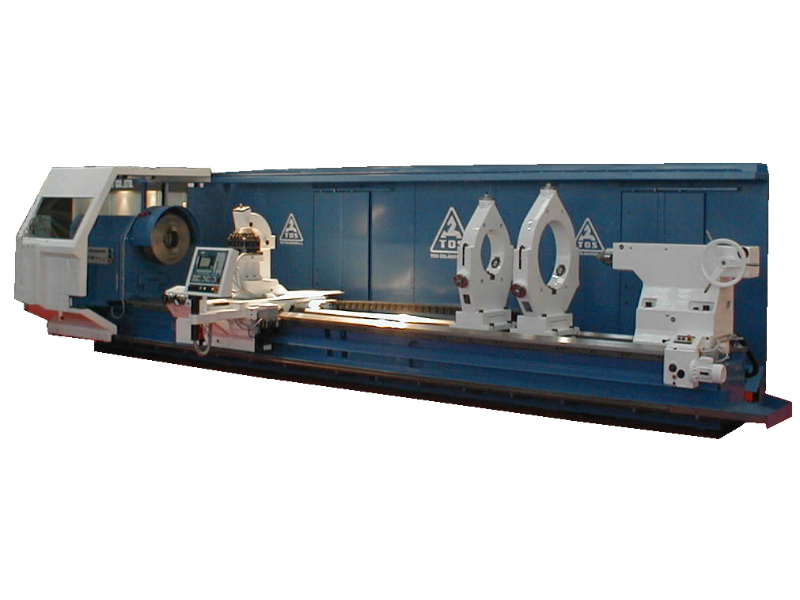
SUA 100 Numeric
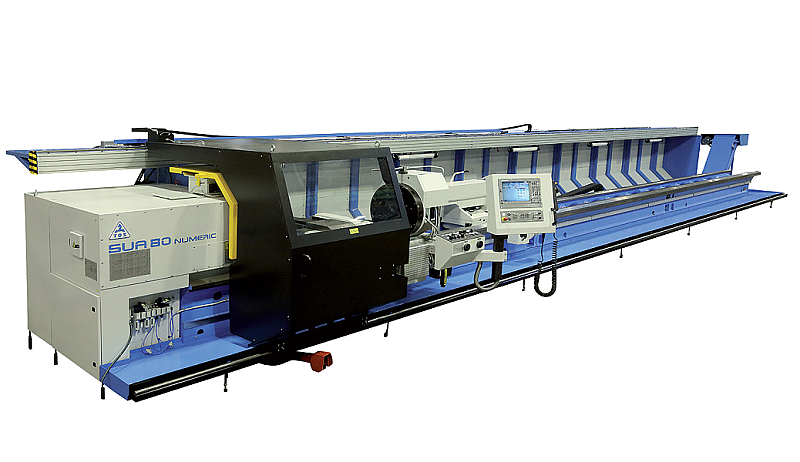
SUA 80 Numeric
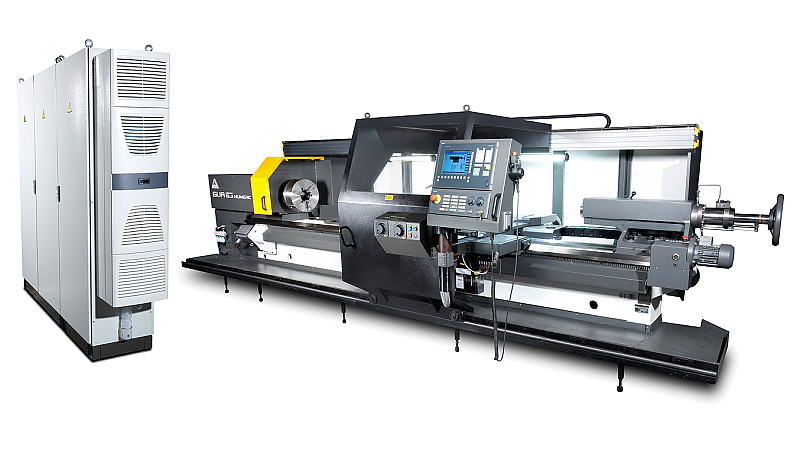
SUA63 Numeric
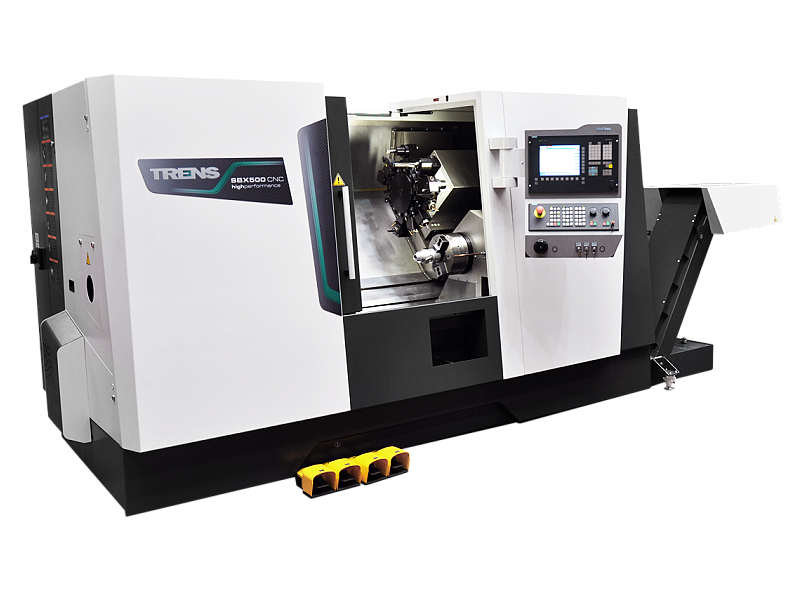
SBX 500 CNC

SBE300 CNC
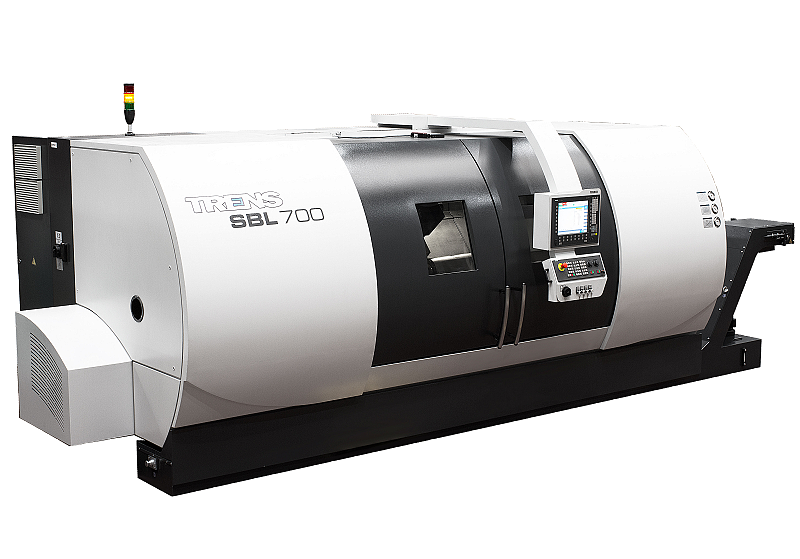
SBL 700 CNC
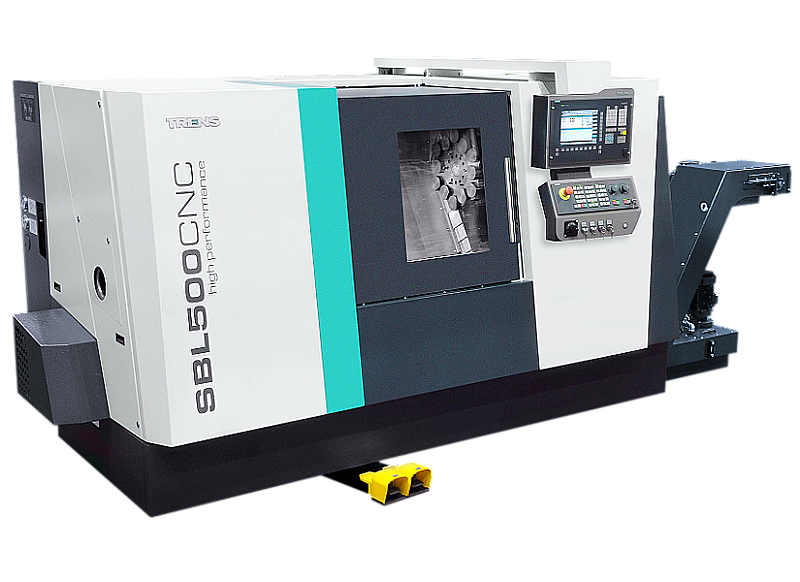
SBL 500 CNC
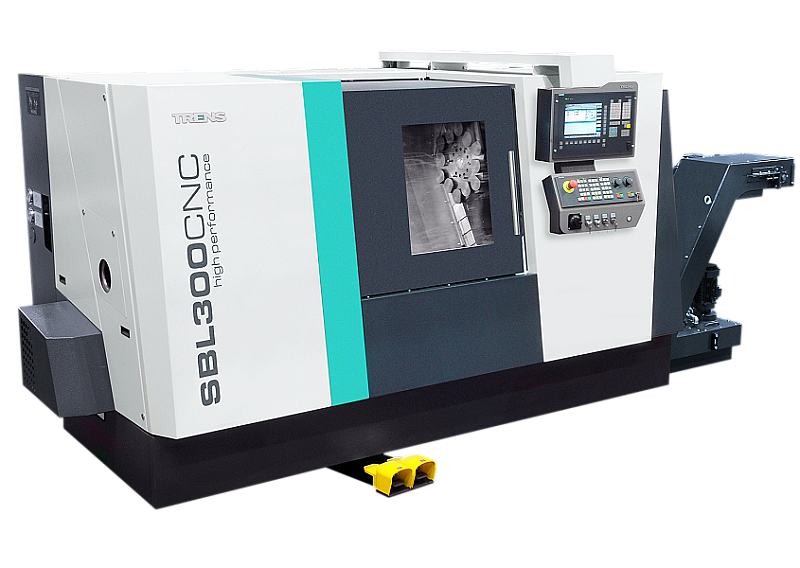
SBL 300 CNC
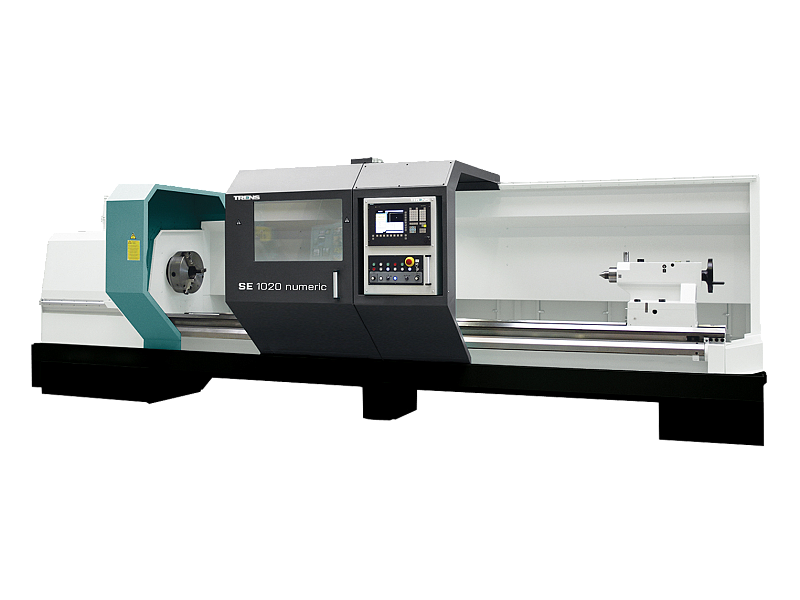
SE 1020 NUMERIC
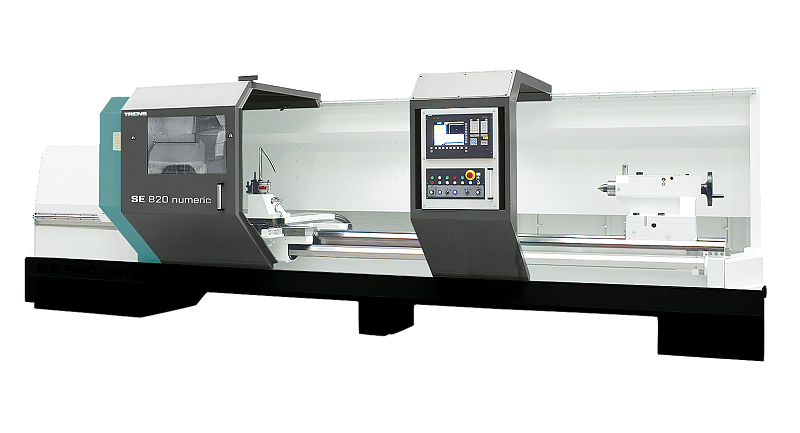
SE 820 NUMERIC
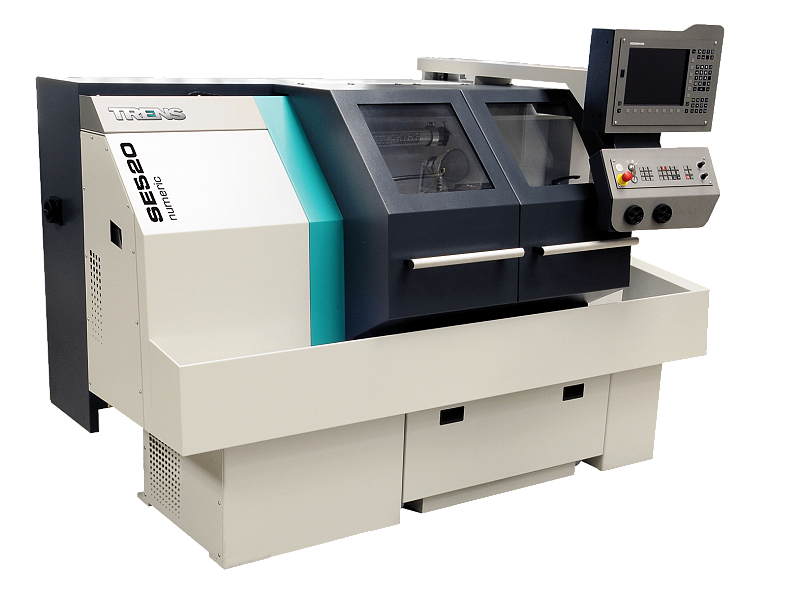
SE 520 NUMERIC
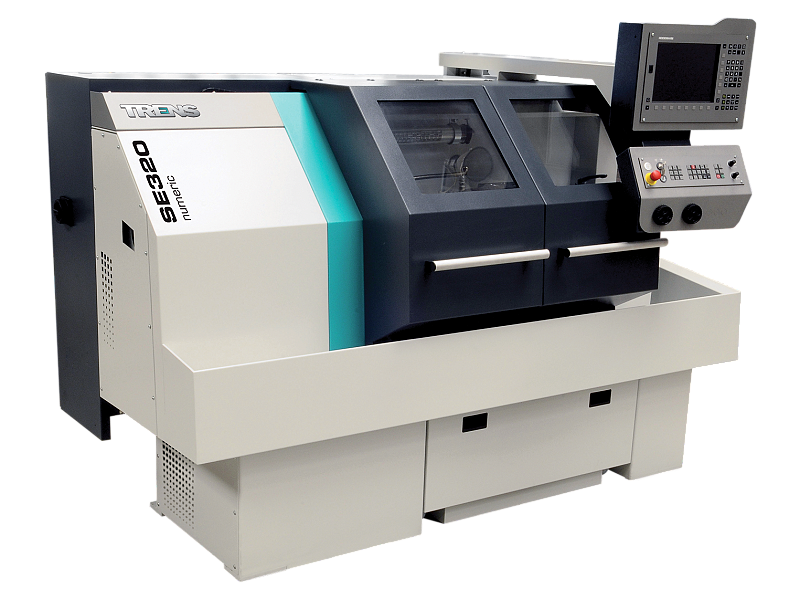